


After thermal stabilization, the board is heated as quickly as possible to the reflow temperature (approximately 250☌). The preheating profile allows you to slowly bring the PCB to a temperature high enough to dry the solder paste (approximately 100☌) while minimizing the risk of thermal stress on the components in the reflow phase. The key to good reflow is a precise multistep thermal profile, as illustrated in Figure 1.
REFLOW MACHINE HOW TO
I’ll finish up with some tips on how to assemble your own SMT boards using the reflow oven. Then, I’ll describe my controller’s hardware and software. First, I’ll cover how reflow ovens work and explain which toasters on the market are best suited to mimic them. In this article I’ll show you how a homemade controller built around a Renesas evaluation board can transform an inexpensive toaster oven into a reflow oven. The ovens cost so much because they need strictly controlled thermal profiles to ensure good soldering and also to limit the thermal stress on the components. Great! The only issue is that reflow ovens cost a fortune, ranging from $2,000 to $1 million. A reflow oven is a well-controlled oven that allows to you cook a PCB with its components and solder all of the pads simultaneously with solder paste. But small packages like 0603 resistors are likely to fly away when soldered with hot air and stick to the soldering iron at the worst time.Ī solution to this problem is to use reflow oven technology just like the manufacturers do.

The components must be soldered individually with either a small soldering iron or a hot-air pencil. It’s possible to solder the majority of SMT components by hand, but it’s painful and time-consuming. High-speed designs (using high-speed digital or radio frequencies) won’t work using large through-hole packages. Many new and exciting components are only available in SMT packages.
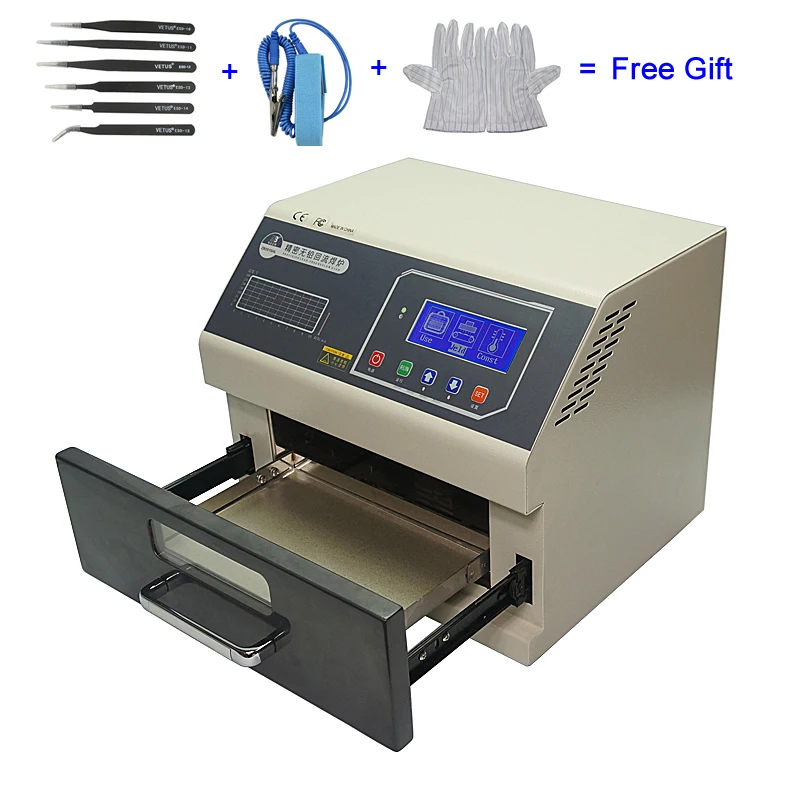
I’m sure you have noticed that SMT is now mandatory for prototypes, even if a project isn’t space-constrained. Robert’s H8/3687-based SMT Reflow Oven Controller transforms a conventional infrared toaster oven into an effective reflow oven that ensures thermal control.įor years surface-mount technology (SMT) has been the manufacturing technology of choice, particularly because it’s less expensive than classic through-hole processes and because of the reduction in board size. Cooling zone: This is the last zone to gradually cool the PCBA and solidify the solder joints.When designing high-speed applications, working with SMT components and soldering by hand can be tedious.The maximum allowable peak temperature limit is determined by the type of electronic component on the PCB assembly with the lowest tolerance for high temperatures (the component most susceptible to thermal damage). It is part of the reflow process where the maximum temperature is reached. Reflow zone: This zone is also called “ time above reflow” or “ time above liquidus”.Thermal soak zone: This is the high temperature zone where the temperature is high enough to melt solder paste so that the component leads get soldered to the pads on the circuit board.
REFLOW MACHINE CRACK
The temperature of the board and all the SMD components is gradually and uniformly raised to prevent any crack to the SMT PCB due to thermal shock.
